Episode 94: Digitized Supply Chain
Augmented Ops - En podcast af Tulip - Onsdage
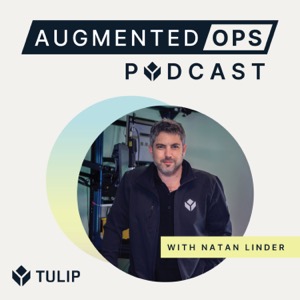
Kategorier:
Augmented reveals the stories behind the new era of industrial operations, where technology will restore the agility of frontline workers. In episode 43 of the podcast (@AugmentedPod), the topic is: Digitized Supply Chain. Our guest is Arun Kumar Bhaskara-Baba, Head of Global Manufacturing IT, Johnson & Johnson.In this conversation, we talk about why J&J puts operators at the center of its strategy, the empowerment effect of frontline operations apps, the evolution of personalized production, and how supply chain becomes an integral part of product development.After listening to this episode, check out J&J as well as Arun Kumar Bhaskara-Baba's social medial profile: J&J (@JNJNews): https://www.jnj.com/ Arun Kumar Bhaskara-Baba: https://www.linkedin.com/in/bhaskarababa/Trond's takeaway: "Operators are the key to the next phase of industrial evolution, that which involves the deep digitalization of manufacturing, its supply chain, production capacity, personalization, and with that the reinvention of factory production itself.Thanks for listening. If you liked the show, subscribe at Augmentedpodcast.co or in your preferred podcast player, and rate us with five stars. If you liked this episode, you might also like episode 21, The Future of Digital in Manufacturing, episode 27, Industry 4.0 Tools or episode 10, A Brief History of Manufacturing SoftwareAugmented--conversations on industrial tech. Transcript: TROND: Augmented reveals the stories behind a new era of industrial operations, where technology will restore the agility of frontline workers. In Episode 43 of the podcast, the topic is Digitized Supply Chain. Our guest is Arun Kumar Bhaskara-Baba, Head of Global Manufacturing IT at Johnson & Johnson. In this conversation, we talk about why J&J puts operators at the center of its strategy, the empowerment effect of frontline operations apps, the evolution of personalized production, and how supply chain becomes an integral part of product development. Augmented is a podcast for leaders hosted by futurist Trond Arne Undheim, presented by Tulip.co, the frontline operations platform, and associated with MFG.works, the manufacturing upskilling community launched at the World Economic Forum. Each episode dives deep into a contemporary topic of concern across the industry and airs at 9:00 a.m. U.S. Eastern Time, every Wednesday. Augmented — the industry 4.0 podcast. TROND: Arun, how are you? ARUN: I'm doing great. How are you, Trond? TROND: Oh, it's wonderful to see you and hear you. I'm very excited. This is a big interview. You have really big responsibilities, Arun. We're going to get to that in a second. But global manufacturing that is a wide, wide topic. ARUN: Yes, indeed. But the bigger responsibility, but more importantly, what we are privileged is how we are impacting the lives of patients and customers around the world with our products. That comes with the privilege to work in the healthcare environment. TROND: Well, I'm glad you said that because as we're sort of tracing, I want to ask you a little bit about how you got to where you are. And I know from public records, at least, that you have part of your schooling in India. So you grew up in India, my assumption is, and you got your computer degree there. You worked in India for a little while for the Tata system. And then you made your way over to Michigan. You have your MBA from there. And then, from what I understand, you then had a bit of a career in automotive and then moved on to Dell. And this brings us to J&J. How did you end up in the U.S.? And how was that journey for you? You've come quite a bit of ways. ARUN: Yes. It's interesting that you asked how I ended up in U.S. For me, it was a choice of either going to Japan or to U.S., And I'm a vegetarian, so for me, U.S. was a better choice. Growing up when you're a kid, you have two years of experience, the decisions that you make, some priorities. TROND: That's funny, but you told me, Arun, that you came here with a briefcase and a $10 bill. ARUN: Yes. I was going to go -- TROND: That's, I guess, not an unusual immigrant story, but it is still quite striking. ARUN: Absolutely. I grew up in a very small middle-class family. So when I landed, I landed with a briefcase and a $20 bill, actually two $10 bills. And out of that, one $10 bill I still have as a reminder of where I started. TROND: Wow. And I cut your career a little short because you have had the opportunity to work in all of the BRIC countries, essentially. And you now manage teams across, I think, at least 28 countries. And that brings us, I guess, up to present day where I was alluding to this, but you have a very wide responsibility. We're going to talk about some of it. Can you tell me a little bit about your current role? ARUN: So, my team supports all the manufacturing operations for J&J across the globe. So we have 100-plus manufacturing plants in pharmaceutical, consumer, medical devices, and vision products. As I mentioned earlier, I am privileged to be in healthcare to serve our patients and customers. We are in 28 countries; my team is spread across. And it's a very humbling experience to really work in a global team and continue to support our operations across the world. TROND: Well, not only that 28 countries, but I understand you operate about 100 manufacturing sites, some obviously state of the art, very big and sprawling, others actually very small or at least mid-size and have all kinds of other issues. And J&J, you know, what is the breadth of products you make? I mean, you make vaccines. You make knees, artificial knees. What else do you guys make? ARUN: This is amazing. I used to work for Ford Motor Company and Dell. Definitely, they are also very strong in manufacturing. However, the manufacturing processes are very similar. It is either assembly process, marketing and manufacturing at Dell. I come to J&J, and any type of manufacturing, you say we got it. Whether you talk about process manufacturing or discrete manufacturing, we have that. So in the pharmaceutical area, we produce biological products where we actually grow live cells and make medicine out of it, as you mentioned, the vaccines and biological products. We also have big chemical products where we actually use big chemical reactions to produce the drugs. In medical devices, we have artificial knees and hips, which are more like a foundry operation. You take a mold, you put it in an artificial knee, and make it happen. And we have sutures that we produce. And in the consumer side, we have different types of liquids, gels, and tablets that we produce. And finally, in vision care is where we produce our lenses in a very high-velocity manufacturing. So if you look at the breadth of the manufacturing processes and products we support, we support almost every aspect of manufacturing. TROND: Well, this brings us to today's topic because we're going to talk a little bit about digitizing these operations, the supply chains, the whole thing, and think about what digital means to all of it, whether it's in pharma 4.0, or indeed, you know, manufacturing and industry 4.0. Can you maybe just kick us off a little bit and say what does digital mean to your business today? And what is your main take on how to approach it? ARUN: The first thing is really I see digital as a means to an end. So if you think about it, it's really why digital is the first and then why digital. We need to be very clearly understanding why we want to digitize. We are in the journey to transform our supply chain so that we can put our patients, our customers at the center of the supply chain and how we can get our products to our customers in a fast, nimble way and in an affordable way. If you think about healthcare, the key is affordability as well as the ability for us to deliver what they need where they need it. And if you think about even the vaccines that we are producing now, we are manufacturing only in some locations, but we have to distribute them everywhere, whether to sophisticated networks like U.S. or developing areas where we don't even have a lot of transportation like Africa. So how do we put the customer and the patient at the center? And how can we actually serve them in a much more faster way and in an affordable way? So that is the why behind our supply chain journey. And digitization is a very critical component of that transformation. How do we provide that end-to-end connectivity so that we can reach our customers and patients? How do we understand what is happening in the markets and react to those things quickly as well as respond quickly using digital? And then ensure that we are delighting our customers beyond just our products, that we have world-class products. But how do we make sure that we are delivering the same customer experience to our patients and customers? So for us, the work from the digital side is how do we build that end-to-end connectivity so that we can reach our customers and we can sense and respond very quickly? And finally, how do we make sure that we significantly improve your customer experience? TROND: I want to pick up on a couple of things, but let me first ask a basic question. I mean, when I think supply chain, I think back to business school where I was teaching for a while, and I think kind of a fairly dry subject that was a specialty subject. You either cared about it, and then you wanted to become an expert and obviously dominate the field. But now you're speaking of it as if it is a much more integrated part of product development, which I think that was certainly taught as two separate courses, even in the very immediate past. But do you think of the supply chain as completely integrated with what you do, what you produce? ARUN: Absolutely. If you think about where the healthcare is headed, if you think about personalized healthcare, if I'm taking a knee right now, we ship like six or seven knees to the surgeons so that they pick the right knee during the operation. And we are getting to a place where we take the picture of the knee, get it back, and make the product, and then 3D print it and give it to the surgeon. Or if you think about how we are personalizing where we are taking the blood from the patient and making the product that is very specific to the patient and shipping it to them. So this whole flow of here is my R&D, and then it goes to supply chain, and then we deliver it versus it is now becoming a connected world where this all comes together. So it's really a very integrated part of product development and supply chain. So we really look at that end to end. And then digital is the one that is actually accelerating that journey. Because I can now connect all of these things as a digital thread and then really push the envelope forward. TROND: But producing for a batch of one, I mean, it's enormously challenging at scale, no? ARUN: Yeah, absolutely. That is the trick, right? How do I produce that batch of one? And if you think about the future, where we can actually get to that and where we can produce batch of one for almost everything that we do is where we are headed. You're right; there are significant investments in terms of our manufacturing operations and the equipment that we need. And there is that balance between the scale that you need to have versus the personalization that is needed. And the balance is I don't think the pendulum can go either one way or the other. But really, we still have a lot more to move to the personalized level. How do we really become a full supply chain so that we can produce that batch of one wherever possible? And look at that from the customer and patient's angle, right? If you have somebody who has a traumatic surgery going on and they have a bone that we need to fix...and it is not the same from one trauma to another trauma. There you can't come back and say, okay, here is a batch of things that I'm producing, and I'm going to give it to you. So the customer expectations are also changing. As a patient and as a consumer, their expectations are also changing. And so we are moving to that batch of one. And how do you do it for different products? And how do you do it for different manufacturing processes is going to be tailored to that business model and then the product. TROND: So another thing that one might assume when we speak about this, because okay, batch of one, but it has to be an advanced system, and it's covering the globe. I mean, historically, if a factory has machinery or systems and digital technologies, it is a very monolithic, massive system. I understand that you have taken at least some care these days to focus on the operators. Why is that so crucial to you? And what does that mean for the kinds of technologies that you're putting into your factories nowadays? ARUN: So that's a very good question. If you think about where manufacturing is headed so that we can drive that flexibility, that approach so that we can quickly respond, we have to relook at our manufacturing operations. That means they need to be a lot more nimbler and a lot more flexible. And a lot of technologies are emerging, and that's all driving. But for us, at the end of the day, it all comes back to that operator. We are here to serve the operator. We call it #operatorrules. Because think about this, we can do all these flexible things. We can bring in automation. We can bring in robots and all of it. At the end of the day, there is an operator at the line who is making it happen. So how do we make sure that we put the operator at the center and then create the experience for the operator so that it makes it a lot easier? If you take any of our plants, the technology is growing very fast. We used to have an ERP system. The operator has to deal with an MES. The operator then has to look at the equipment interface that the equipment provider has given. Now I'm coming from technology and saying, okay, here is the smart glass. Wear the smart glass, and you can look at everything. Think about the operator, how complex we have made the operator's life. So we are trying to take a step back and say, how do we, first of all, make it simple? Number two is how do we empower them? So far, we all said that, oh, technology is either manufacturing engineering or the OT or IT people. We held the keys for the technology. But how do we really empower the operators so that they can make it flexible and then they can make it nimble? So that gives you the velocity that we need at our manufacturing operations. TROND: It's striking when you think about at least digital technologies now clearly. There have been machines in factories for centuries. I mean, that was sort of the various industrial revolution. So there have, of course, been machines that could be operated by operators to some degree. But the kind of control and the detail-level customization that's now becoming possible doesn't come naturally, does it? It takes a lot of attention to create those kinds of platforms. How do you see that evolving? For example, we said you have over 100 different sites, some of them large, others much smaller; what sort of approaches are you taking to experiment with these solutions? ARUN: So it's purpose-driven experimentation. Because to your point, when we have these large, fully automated factories, the key is how fast I can introduce new capabilities into that operation. Whereas when I go to a middle-tier factory with semi-automated or not as much automated, it is a very target problem-driven. I have an OEE problem. Let me figure out how do I experiment to bring the technology. But at both the spectrums, the key is to make sure that there is a good, robust architecture principles. There is good, robust security, and then there is a good data architecture. But from a solutions point of view, how do we make sure that these are modular? Think about the mainframe days where you need to know all those to run the application to now you have apps on your device. So how do we break these monolithic technologies that are running the operations into smaller apps by bite-sized chunks that we can actually deploy very quickly or pull it out? And that gives me the flexibility to say for a large site; I'm going to deploy all these 100 apps so that they can run it as a suite. Whereas when I go to a smaller site, I might only deploy two of those applications for a specific problem. So it's kind of like really breaking down by, number one, by purpose. Number two, having a good consistent architecture. And number three, really breaking these monolithic things into smaller apps and nimble apps that we can drive. TROND: I know that you've tried some of Tulip's solutions. Tulip is an app system. But clearly, the bar to completely replace any number of advanced technologies that have developed over literally decades is not done overnight. How do you see the journey that app developers on the manufacturing shop floor...what sort of journey are they going to have with you to prove themselves over time to gradually solve many of these very ambitious problems? I mean, you describe them pretty eloquently, but they're different in each factory, like you pointed out. And we're dealing with operators, some of whom are very advanced and have taken all kinds of industry 4.0 courses and others who have not. So this is a bit of a journey. ARUN: Yeah, it is a journey, but there are similarities in this journey. If you think about maintenance of the equipment, it used to be a stronghold of those engineers that are sitting somewhere, and they get to the equipment when there is help needed. Look at where we are now. With operator asset care, we are empowering the operators to own that equipment and drive it. So that is the same journey that we have to go through from the digital side. And the key is, first of all, making sure that we have platforms like Tulip and others that help us to be able to quickly develop those apps, of course, in a very consistent framework. Especially for us when we are in a regulated industry, some of those framework and validation things become extremely critical. How do you set those boundaries? The second thing is educate the operators so that they feel empowered that they own the work that they are doing, and they can shape it in the way they need to do it and to continue to train them. And then the third level is to really train the rest of the organization. The management and then the operations leaders all need to be digitally savvy to drive that and then see the value. So it is a journey, but you need to be very clear about why we are doing it and putting the operators at the center and helping them. The thing that is going to help us is this whole COVID pandemic situation. If you think about the digital savvy of almost the entire world, it has significantly improved. Every operator, whether we like it or not, yeah, they might not have a degree, but they know how to order their Uber Eats. They know how to use an app. So we are seeing digital literacy coming up very fast. So this is a great opportunity for us to drive that transformation. But you're right; it is a journey. TROND: But you also mentioned regulated industry. I mean, to what extent can some of these apps kind of slide in between the cracks and do stuff that was never covered by regulation? And to what extent do you actually need to take very, very good care that you are, I guess, also updating the regulations and knocking on the doors of governments and telling them that "Look, there's an app for this too."? [chuckles] And we need to upgrade the regulatory framework to take that into account. So it seems to be a bit of both. ARUN: Yes, you absolutely hit the nail on the head. You need to do both. One is, first of all, have a good, robust architecture. That's why the platforms like Tulip will need to ensure that the architecture is robust so that it has enough control so that we can drive this validation and qualification, those things, and giving the parameters of the freedom for the operators within those constraints. And let's not forget cybersecurity, which is a huge thing, especially when we come to the OT cybersecurity as well. And on the other side...sorry. TROND: No, no, go ahead. On the other side... ARUN: On the other side, we need to continue with the regulators and work with the regulators to make sure that they understand what we are doing. We are now working with the regulators to educate them on real-time release. How can we actually use the data rather than having to produce these samples and batches as opposed to relying on continuous data that is coming that shows that your process is in compliance? So working on both sides with the framework so that it is robust as well as regulators to make sure that they understand how the technology is transforming. At the same time, the compliance is improving. Think about it, when you're doing samples, one, you're taking one sample from a batch. But when you're doing continuous sampling, you have the whole sample, whole product batch data you have in your hands. So we'll continue to work with them to make sure that the regulators are also coming with us on that journey. TROND: How is pharma 4.0 going? I mean, the acronym is the same as industry 4.0. Is 4.0 actually happening, or are we still in 3.0? ARUN: In pharma-world, I would say we still have 2.0 to 3.12 to 3.33. And there are some great examples where we have the 4.0 when I talk about what we are doing with the personalized solutions when we talk about how we are bringing IoT to the forefront, how we are doing real-time release with digital twins of our whole process. Now we have digital twins, even for bioreactors, which are very difficult to characterize. So yes, the journey is there. The key is to keep in mind why we are doing it to really make sure that we have the patients that are waiting for our products in mind and then really transform around to support them. So the journey is continuing. Yes, there are very good examples for pharma 4.0. But are we there yet? No. But is everybody working together to get there? Yes. TROND: Let's talk a little bit about this operator and the training of an operator because training the workforce is something I ask a lot of the people who come on this podcast about just because technology is one thing but training people on the technology to implement it in a fruitful way is a whole other challenge. What approach are you taking at the whole J&J complex when it comes to training your existing future and even training your ecosystem around you? ARUN: A couple of things there; one is, first of all, making sure that you start with the user experience in mind and design everything from there. So you need to start with the design aspect. The second thing is how do we make it simple? The more simple you make it, the less training. How many people are getting trained on how to use an iPhone? So really, how do we make it simpler? But actually, in the future, I'm thinking...and this I actually got from one of your podcasts, Trond, is, are we going to get to a point where there is no interface? So can we get our apps to a state where there is no interface, then your training becomes a lot more part of the evolution rather than you have to go; oh, now I need to learn this, and I need...no, it should be so intuitive. It's like gesturing with my hands. So how do I get to that state? Hopefully, that state comes in soon, as you've been discussing with some of them. But for me, it is really how do we keep on making it so simple that it becomes intuitive? And it starts with the design, where you put the operator at the center and design around the operator. TROND: Can we talk a little bit more specifically about the digitized supply chain? Because it is such a core to what you're up to. And I know that there are some characteristics that you care about the most one of them I think you mentioned to me was being very responsive. But what are the priorities when you are redesigning a supply chain? What are the kinds of things that are top of mind for you? And where do you start? ARUN: You start with the customer experience. How do we make sure that that is clear on how it is impacting the customer experience? Now to help with the customer experience, how do we drive that responsiveness in your supply chain so that you can respond very quickly to what is happening at the demand side, the customer side, and then link it back? Then the next one is really the resiliency. How do we build that resiliency in supply chain so that we can react very quickly? If there is one thing that COVID taught us is that resiliency in our supply chains actually helped the world in one way to survive this pandemic and continue to survive. So how do we drive that resiliency in the supply chain? TROND: What do you think about these very traditional concepts that have been part of...and, you know, you had the start of your career in automotive. Lean management is something that everybody wanted to copy, and the Toyota processes and a lot from the country you chose not to study in [laughs] essentially because you weren't convinced they were vegetarian enough. But anyway, what do you think about the heritage from lean and mixed in with some of the agile tradition from software? Is that altogether creating a new paradigm? And what does that look like, and who's describing it? If you would maybe describe where some of your influences come from when you are designing such a large organization around these principles. ARUN: At the heart, the lean principles and agile principles are still really valid. Like, if you think about lean, what it is saying is think about the floor, eliminate the waste, and continue to improve and zero defects as possible. So that mindset has to be there for us to even look at digital. What digital is doing is actually helping us to implement lean even faster. How do you get there? Now, from responsiveness, and we talked a lot about the responsiveness, and reacting, and resiliency that requires this agile mindset, this traditional boundaries of I'm going to go from plan, source, make, deliver. This is becoming a network. The only way you can survive in that network is having that agile mindset where we bring people together very quickly, get the problem solved, deliver that MVP, and don't look back and then move on to the next one. So the agile principles around bringing the teams together very quickly to focus on the key priorities and delivering on the MVP aligned with the lean thinking to make sure that there is no waste and we are really getting the floor done actually is a great combination of these two. And these are the two things that need to come together even for us to roll out the digital solutions very quickly in our operations. And COVID has been a great example if you think about how we came together to deliver a product for the instruments in a very quick way across the world in a virtual way. It has been a great example that shows that it can be done. So that's where the lean foundations and then the agile mindset are extremely critical, even for us to drive this digital transformation. TROND: If you think about how this was built, what are some of the best influences that help you along the way? We talked a little bit about startups that bring the app mindset and maybe some of the agile thinking. It doesn't necessarily come from startups, but certainly, it does exist with startups. Where are these industry practices that you are increasingly embodying at J&J? Where do you think they come from? ARUN: Actually, they come from many places. And for startups, really one of the places where we can actually see how their mindset is there in terms of test and learns, and learning from failure, and more. And even I'm looking at some of the journeys like how companies like Tulip are evolving as well. Especially those companies from a startup to accelerating phase, that's where we are seeing a lot of the learnings that we can learn. And one of the big things that we at J&J look at is how can we look at our CEO and saying, "Hey, we need to act like a 135-year-old startup."? So how do we actually look at it? And to your point, where we are looking for, we are looking for everywhere; one is really those startups. But more importantly, those startups that got that first phase and are now accelerating, that's where all the processes need to come together. And then, at the end of the day, we still have to be reliable. And we are in a regulated industry. So how do we make sure that the patient safety, product quality are the top priority and our processes are reliable? That's where the established companies also help us on how we continue to drive that. TROND: Yeah, because that's what I guess I wanted to drive to because there is an established idea in the established industry to look for industry best practices. And in the manufacturing space, there are these lighthouse projects. Companies on their own might have lighthouse projects that are especially good. And the World Economic Forum has lighthouse factories. In fact, they have designated places around the world where they have tracked and figured out that they are of sufficient quality to put up as inspirational lighthouses for others. What is your view on how well that works as a practice? For example, you have 100 sites. Is it possible to tell one site to become more like Site A? Because look at site A how well they're doing. Isn't that also a bit of a challenging message to communicate? ARUN: Yeah. TROND: No one likes to be like, all right, I understand. [laughs] My golf swing is not up to par, I get it. I need to look at my neighbor over here. It's not always a fantastic message. ARUN: [laughs] But speaking of that, actually, we have five sites that are lighthouse sites. And we have one that is going to come up with one of the projects that we're working on as well is in one of the sites with Tulip for the lighthouse site. But the thing is, knowledge grows by sharing. The more you share, the more you're going to grow the knowledge and the faster the adoption is going to be. You're absolutely right. It does not mean that just because this is a lighthouse site, they are at a pedestal, and then everybody else is in another place. I actually look at it the other way around. What did those lighthouse sites do that we can actually copy and paste, so I don't have to reinvent? And then I can focus on something else as well. So the lighthouse sites are helping us to really share that knowledge so that we can learn from one another. We can build on it. And then we eliminate the need for us to redo the things that they have gone through. But you're absolutely right; that doesn't mean that those are the only sites that are doing everything and everybody else is not. But sometimes, the copycats that are coming behind the lighthouse might be the best of things because they can get lighthouse practices and implement and then really show that they can actually transform their manufacturing operations much more faster. TROND: Well, and that's true in the history of manufacturing that you can actually leapfrog. It is still a field where if you do many things right, you definitely make a difference. I wanted to shift tact a little bit, Arun, and move to coming years. What are some of the industry developments that you are the most excited about? So we've talked generally about digital. We've talked about personalization. What are some of the things that are going to be most crucial to get right and even just like in the year ahead? It's been a very...it's been a wild ride in the last 12 to 15 months. What's going to hit us in the next year, and what are you focused on? ARUN: So let me break it into a few different areas. One is purely from the technology side of it. If we look at how 3D printing is going to evolve and how it is going to help us to change significantly, how the digital twin and digital threads that are coming up fast that we can actually connect. And then, more importantly, how the machine learning and AI models that are coming up that help us to be responding very quickly. So I'm very excited about those areas, how 3D printing is transforming our operations, how we are able to bring digital twins, digital thread, and machine learning to really drive that end-to-end thread all the way to the customer. The second area is, from a mindset point of view, is how resiliency and responsiveness has become kind of like a norm. If you think about the COVID pandemic, what it has done is how that resiliency and responsiveness has become a norm. So how do we actually drive that and don't lose that as we come out of the pandemic and then go forward? And the final one is I'm going to go back and harp on the culture side of it. How do we drive that culture where we let operators be empowered and learn from it and let them be the kings? And we also have the operator hashtag #operatorrules. And we support that culture change, the digital change, and which is really going to be accelerated because they are becoming more and more digital savvy. So there is the technology aspect. And there is actually the responsiveness. And finally, how do we drive the digital savvy across the organization? TROND: So my last question, and I don't know how fair that question is in the context that you're in, because I could imagine that given the amount of factors that are moving at any given moment, very long-term thinking seems perhaps a little farther away from your everyday life. Because there are so many things that could go wrong literally every minute. But if you permit yourself and me to think a little bit longer term, towards the next decade, are these things on the digital side, you know, digital twins, and AI, and machine learning, and 3D printing, as this decade moves to a close, are there other things on your horizon as well that will even more drastically transform the landscape? I mean, are digital factories going to be really coming into the scene and really transforming the way? Are we going to recognize a factory even in the next decade? Or am I kind of overblowing this, and things are just fairly complicated, and it's going to take quite a long time to shake out and integrate all these technologies with all of the workforce challenges and cultural challenges that you just pointed out? ARUN: Imagining the future, first of all, I really love the idea of almost no interface, intuitive use of technology. Can we get to that? That's one. The second thing is, yes, there will still be big manufacturing areas. Some of them are tied to the physics and biology, so we cannot change, but everything else can actually significantly change. And if you think about can we actually do a factory in a box very quickly for vaccine production in a developing world that cannot afford and we deploy it very quickly? So will we get to a point where it becomes more of Lego blocks that we can assemble very quickly and get it up and running and everything has an equal and digital model that we really don't have to worry about it? It is not about the digital twin of my operations. But if I take the digital twin of my patient's body and the digital twin of operations, think about how easy it is for me to actually respond to that personalized request or personalized medicine. Since you let me imagine and let my thoughts flow a little bit more broadly, it's really bringing the digital equivalence. So can I actually take my digital equal and to respond to the digital twin to get the personalized product for me either in a batch of 1 or even maybe a batch of 10 if batch of 1 is not possible? So the factories of the future, yes, some of them might not significantly change, but most of them will be that flexible way to bring them together for specific product or specific customer and being able to re-assemble very quickly to do something else. And then the intelligence, can it move to the equipment so that the equipment itself can rearrange itself based on the customer base? But then, what is the implication to the workforce? And what is the implication to the operators? So this way of getting those operators to be a lot more digital savvy and really helping to manage this complexity will be a great foundation. But at the same time, that is something that we all need to watch. Yes, all of this can happen. But we need to watch for how do we bring our people together? TROND: Yeah, and I could just imagine putting myself back in my old government days, scratching my head about self-regulating systems in the medical field, right? [laughs] ARUN: Yes. TROND: That would seem to be a little bit of a challenge as well. So there are so many interesting challenges. But it seems to me that even if you are occupied every minute with operational challenges and even just digitizing a supply chain without fundamentally changing its logic, it's going to take all men and women on deck. It's a cultural challenge. It is not just a technology challenge. ARUN: Absolutely. It is. It is a cultural challenge. TROND: Well, look, it's been fascinating to hear, and I hope I can check back in with you. It seems to me that if we had had this interview just even just 15 months ago, some of these challenges might have looked a little bit less rosy, and we wouldn't have been discussing about the next decade. I'm assuming that a lot of things for you in your business have really, I guess, opened up throughout this pandemic. Is that right? ARUN: Yeah. TROND: Some of these opportunities just weren't there before. ARUN: Absolutely. A lot of the acceleration...first of all, we are privileged to serve our patients. And we have a big part in helping the world get through the pandemic, our vaccine. And even how we have brought in digital twin into our vaccines in a very faster way was enabled by the pandemic situation. The whole digital acceleration of some of our solutions that were sitting on the shelf for almost six to nine months, the demand for them grew up within the first few months of the pandemic. So the digital acceleration of our operations has happened. The third thing, as I said earlier, is the digital savvy of our day-to-day citizen is helping us to bring these much more faster to our patients and customers around the world. TROND: That's a very interesting statement. Because when you cannot innovate faster than your end client, then you're really dealing with the total ecosystem here. You actually depend on your end client to be caught up with all of these technologies. It's a fascinating challenge and probably very important too because there isn't a little bit of an insurance policy there, no Arun. Because if you cannot be more advanced than your end user is, at least you have the time to, or you have to take the time to educate the end user and get their real feedback on what needs to happen. So that leaves me on an optimistic note, and if you have any last statement...I certainly thank you for your time. And if you have a last challenge, you know, there are so many challenges where you could launch, but if you think to your fellow industry executives, what is the one thing maybe you want to leave them with what you think is a shared challenge that people should focus more on in industry these days? ARUN: Keep the operator at the center #operatorrules. Let's make sure that we empower them. We help them to be as digitally savvy as possible. That will actually help us to move these needles much more faster. TROND: Arun, I thank you so much. It's been a pleasure. And I hope I can invite you back someday. ARUN: Definitely. It has been great, Trond. TROND: You have just listened to Episode 43 of the Augmented Podcast with host Trond Arne Undheim. The topic was Digitized Supply Chain. Our guest was Arun Kumar Bhaskara-Baba, Head of Global Manufacturing IT at Johnson & Johnson. In this conversation, we talked about why J&J puts operators at the center of its strategy. My takeaway is that operators are the key to the next phase of industrial evolution that which involves the deep digitalization of manufacturing, its supply chain, the production capacity, personalization, and with that, the reinvention of factory production itself. Thanks for listening. If you liked the show, subscribe at augmentedpodcast.co or in your preferred podcast player, and rate us with five stars. If you liked this episode, you might also like Episode 21: The Future of Digital in Manufacturing, Episode 27: Industry 4.0 Tools, or Episode 10: A Brief History of Manufacturing Software. Augmented — conversations on industrial tech.Special Guest: Arun Kumar Bhaskara-Baba.